推荐文章
recommended articles
- 电缆串联谐振技术助...
- 电力安全无小事,电站...
- 第79期高压试验技术...
- 300kw变压器感应耐...
- 直流高压发生器新升...
- 天津强维电力工程采...
- 35kv串联谐振等承试...
- 10kv配电房预防性试...
推荐案例
《电力装备制造业数字化转型实施方案》发布
-
责任编辑:
人气:
发表时间:2024-11-06 13:42:56
10月23日,工信部发布的《电力装备制造业数字化转型实施方案》指出,到2027年,电力装备制造业数字化转型取得明显成效。
一是数字化水平明显提升,电力装备制造业重点企业关键工序数控化率、数字化研发设计工具普及率分别超过75%、90%。二是标杆引领作用持续增强,建成15个左右国家级智能工厂、5家左右数字领航企业、10个左右5g工厂。三是支撑服务能力不断完善,建设3个左右电力装备制造数字化转型促进中心,培育10个左右特色专业型工业互联网平台、优秀凯时尊龙官网的解决方案服务商。到2030年,电力装备制造业规模以上企业在研发设计、生产制造、运维服务等环节完成深度数字化改造,人工智能赋能效果明显,数字化改造达到世界先进水平。
以下为原文
工业和信息化部关于印发《电力装备制造业数字化转型实施方案》的通知
各省、自治区、直辖市、新疆生产建设兵团工业和信息化主管部门,有关中央企业,有关行业协会,有关电力装备生产企业: 现将《电力装备制造业数字化转型实施方案》印发给你们,请结合实际,认真贯彻实施。
工业和信息化部
2024年9月5日
电力装备制造业数字化转型实施方案
电力装备是国民经济发展中基础性、战略性产业之一,是加快能源绿色低碳转型、保障国家能源安全的重要物质技术基础,是落实碳达峰、碳中和战略的重要保证。加快行业数字化转型,是提升电力装备研发制造水平、保障质量可靠性、提升产业链运行效率的重要举措,是推动电力装备制造业高质量发展的必然要求。为深入贯彻习近平总书记关于推动电力装备发展的重要指示精神,认真落实国务院关于制造业数字化转型行动总体部署,加快实施《制造业数字化转型行动方案》,推动电力装备制造业数字化转型,制定本实施方案。
一、总体要求
以习近平新时代中国特色社会主义思想为指导,认真贯彻落实党的二十大和二十届二中、三中全会精神,立足新发展阶段,完整、准确、全面贯彻新发展理念,构建新发展格局,加快推进新型工业化,深入实施能源安全战略,锚定碳达峰、碳中和目标,推进能源绿色低碳转型,以推动电力装备数字化转型为主体,坚持问题导向、需求导向、实用导向,强化软硬协同,以新一代信息技术与电力装备制造业深度融合为主线,以智能制造为主攻方向,分类、分级推进数字化转型工作,形成场景、工厂、产业链和产业集群立体式数字化发展路径,以数字化转型提升电力装备产业基础能力和产业链现代化水平,不断推进电力装备高质量发展。
到2027年,电力装备制造业数字化转型取得明显成效。一是数字化水平明显提升,电力装备制造业重点企业关键工序数控化率、数字化研发设计工具普及率分别超过75%、90%。二是标杆引领作用持续增强,建成15个左右国家级智能工厂、5家左右数字领航企业、10个左右5g工厂。三是支撑服务能力不断完善,建设3个左右电力装备制造数字化转型促进中心,培育10个左右特色专业型工业互联网平台、优秀凯时尊龙官网的解决方案服务商。到2030年,电力装备制造业规模以上企业在研发设计、生产制造、运维服务等环节完成深度数字化改造,人工智能赋能效果明显,数字化改造达到世界先进水平。
二、重点任务
(一)加快关键环节数字化转型
1.研发设计数字化。在成套发电装备、输配电装备产品设计、工艺优化等环节,融合运用虚拟现实、智能算法、大数据等,实现零部件到整机的多方协同设计。利用载荷分析工具、数值模拟技术,开展风电叶片、燃气轮机叶片、水轮机转轮、变压器等智能设计,提升设计效率。加强电磁热力流等多场耦合仿真工具在电机转子、励磁设备、变压器、开关保护电器等产品设计中的应用。
2.生产制造数字化。支持电力装备整机企业建设协同制造平台,促进生产制造过程智能化和高效协同。面向电力装备整机及零部件企业开发生产资源库、工艺数据库和排产模型库,构建智能计划排程系统。在成套发电、输变电装备生产过程中,推广机器人自动焊接技术,提高焊接质量、效率。加快成套发电装备制造企业建立定转子线圈、冲片、叠片智能制造生产线,提高生产效率。在大型发电装备等复杂产品装配中,探索大空间数字测量设备和虚拟装配技术应用,缩短装配流程和周期。
3.质量管理数字化。支持企业建设电力装备整机制造全生命周期质量管理平台,提高装备制造整体质量管控水平。加快运用人工智能图像识别、大数据分析等技术,开展产品表面缺陷、金属部件焊缝、零部件尺寸等检测和分析。探索建立电力装备企业产品数字身份管理,利用工业互联网标识解析技术,实现批次性风险产品快速精准定位和质量追溯。引导龙头企业建设产业链质量数据平台,促进质量信息互联互通,提升产业链质量协同发展水平。
4.供应链管理数字化。加快企业依托新一代信息技术,开展采购寻源、采购计划、订单确认、物流运输、合同结算等,加强供应链流程互联互通。鼓励电力装备制造企业和电网、电站、物流企业等进行深度合作,建设共享共用的仓储管理、物流配送数据资源平台,提高库存周转效率。引导重点企业建设供应链风险监测和预警系统,提高供应链风险分析研判能力。搭建重点电力装备全生命周期绿色供应链管理平台,加快建设绿色供应链。
5.运维服务数字化。加快在风光水火核等大型发电装备以及特高压输变电装备领域运用数字孪生、智能传感技术,对机组进行远程监控、故障诊断和预测性运维服务等。建设汽轮机叶片等电力装备高温热部件寿命监测与管理系统,评估部件工作状态、温度、应力和寿命。建设满足特定地理和气候环境下的风电装备智能运维平台,利用物联网、大数据、ai视觉、无人机等技术,对风电机组、风机叶片等进行远程状态监测、故障预测。
6.节能管理数字化。推进数字技术和绿色技术在电力装备设计、制造中的融合应用。引导电力装备企业建立完善的制造过程碳排放数据计量、监测、分析平台,实现企业能碳精细化管理。支持重点耗能电力装备上云上平台,对装备运行能耗进行实时监测。对光伏、风电机组等清洁能源装备开展碳足迹核算,鼓励行业协会、龙头企业建设电力装备碳足迹相关数据库。
(二)夯实数字化转型基础
7.健全标准体系。构建完善的电力装备制造业数字化转型标准体系,制定电力装备制造工业元数据、系统可靠性要求等基础通用标准,以及远程运维、质量管控、个性化定制等重点场景标准。重点编制电力装备制造数字化转型评价标准,推进产品主数据标准生态建设,加强与两化融合管理体系、数据管理能力成熟度和智能制造成熟度等国家标准体系的融合衔接,加快标准宣贯和应用推广。
8.强化评估诊断。建立电力装备制造数字化转型服务平台,引导电力装备企业广泛开展线上自评估。指导行业编制电力装备制造数字化转型评估诊断工作指南,规范评估服务流程。鼓励地方政府遴选电力装备制造数字化转型评估服务商,“一企一档”编制评估诊断报告,“一企一策”精准制定数字化转型实施方案。
9.夯实网络数据基础。引导电力装备制造企业积极开展内外网络改造和装备联网升级,优化网络基础设施,提升装备联网率。鼓励企业实施工业互联网安全分类分级管理,提升网络安全防护水平。指导企业开展重要数据识别与目录备案,加强数据分类分级保护,落实风险评估、监测处置等要求,提升数据安全保护能力和水平。
10.推动制造装备改造。加快制造装备更新改造,开展数控机床与基础制造装备、增材制造装备、工业机器人、工业控制装备、传感与检测装备等智能化改造升级。推进工厂内无人车辆、巡检机器人等装备部署应用,提升生产过程感知、决策和执行能力。引导输配电装备企业探索柔性生产、个性化定制等制造新模式。加快发电装备控制系统、风资源仿真设计软件等工业软件攻关突破。
(三)构建数字化协同转型生态
11.加快链式转型。引导龙头企业加强中小企业数字化转型合作,带动产业链中小企业“链式”转型。支持龙头企业制定产业链上下游协同改造方案,“链式”开展数字化改造,提升产业链整体数字化水平。鼓励龙头企业结合自身转型经验,打造可复制推广的典型凯时尊龙官网的解决方案,为上下游企业提供产品全生命周期、全产业链统一的数字化改造服务。
12.推动集群转型。联合政产学研等各方力量,打通产业集群内的数据链、创新链、信息链和服务链,形成数字化转型合力,推进集群内企业面式转型。在电力装备产业聚集地,开展工业互联网平台、数字化服务商进园区、进基地、进集群。在电力装备先进制造业集群鼓励组建数字化转型联合体,为集群内企业数字化转型供需对接、应用推广等提供便利。
13.培育优质服务商。聚焦电力装备制造研发设计、质量管控、运维服务、全生命周期管理等关键环节,培育综合型凯时尊龙官网的解决方案服务商。开展电力装备行业数字化转型服务商分类分级评价规范标准研制,实施数字化转型服务商分类分级评价规范标准贯标试点。引导服务商提升全流程服务供给水平,建立咨询策划 路径规划 实施监督 跟踪评价全栈式服务能力。
三、组织实施
(一)完善工作推进机制加强部门协同、央地联动,营造良好发展氛围,形成推动电力装备制造业数字化转型合力。各地区加强与本方案的工作衔接,统筹推进各地区电力装备企业数字化转型重点工作。鼓励地方政府组织企业线上线下开展数字化评估诊断,指导企业分类分级开展数字化改造。指导编制电力装备制造数字化转型典型案例,加快案例宣传推广。
(二)强化企业主体作用强化企业在数字化转型中的主体地位,鼓励企业加大数字化转型资金投入,用于开展新型技术改造、数字技术升级和应用创新。引导企业加强员工数字技能培训,培育数字化转型专业人才。支持龙头企业开展“链式”转型,带动上下游企业数字化协同改造,充分发挥标杆示范企业的引领作用,实现大中小企业协同转型。
(三)提升服务支撑水平依托行业协会、科研院所、高校等机构,建设电力装备制造数字化转型促进中心,为企业提供诊断、咨询、评估等服务。加快数字化转型服务商迭代开发高质量数字化凯时尊龙官网的解决方案,培育带动性强、可复制可推广的典型经验。通过特色活动,加强行业交流和信息共享,为电力装备制造业数字化转型营造良好氛围。
附件:典型场景
典型场景
一、研发设计1.典型场景:大型发电机组数字化设计
痛点:在传统的发电机组设计中,缺乏多方设计协同能力,设计方、制造方、服务方的设计软件存在差异,设计规范不统一,设计效率较低。
改造目标:通过设计平台的统一集成,打通各方的设计过程数据,形成一致的设计版本,实现设计过程数据、模型数据的共享共用,从而提升研发设计效率。
实现方式和需要条件:通过运用统一的研发设计工具,使设计方、制造方等多方之间规范定义和传递产品研发设计、工艺设计等各阶段成果和数据,实现多专业协同设计,提高跨部门合作效率。同时对三维软件进行深度开发,运用大数据和人工智能技术,将机组三维制造信息与三维设计信息共同定义到产品的三维模型中,实现高度集成。最终形成唯一的设计模型数据源,推动企业高效开展设计仿真,和产品性能、可制造性、可装配性等分析,实现设计、工艺、制造协同。
2.典型场景:高压气体开关数字化设计
痛点:高压气体开关长期以来存在电弧物性参数不全、开断数字化设计方法不准、温升与机械可靠性模型不全面、精密测试手段不足等难题,亟待突破。
改造目标:建设高压气体开关数字化设计(仿真)平台,引领我国高压开关由经验试错向可预测性数字化设计变革。
实现方式和需要条件:研究燃弧平衡态及弧后非平衡态多组分气体电弧物性参数计算方法、精细光谱辐射计算方法、以及弧后临界击穿场强计算方法与实验装置,建立气体电弧基础参数数据库,支撑开关电弧精确建模。建立高压气体开关电弧开断全过程精确模拟方法,提出适合工程应用的弧后热击穿及电击穿判据。建立针对高压气体开关的电磁热流全耦合仿真模型,建立基于虚拟样机技术的高压气体开关开断过程动力学仿真方法。建立融合高速摄像、动态压力传感等技术的综合测量平台。
二、生产制造
3.典型场景:特高压输配电装备智能化制造及检测
痛点:特高压输配电装备制造涉及零部件种类繁多、异形零件占比大,面临装配工艺复杂、装配自动化技术难度较大、装配工序自动化水平低等问题。
改造目标:导入自动化产线,实现产品智能化装配制造和检测。
实现方式和需要条件:应用传感器、激光测量与定位、机器视觉识别、伺服耦合等系统,通过机器人控制、三维视觉算法、数字孪生、5g等技术,实现机器人自动上下料、自动加工装配、自动检测试验、自动包装发运、自动配送入库等工序的数字化管控,保证产品制造的质量一致性,提高装备的装配制造效率,提升产品质量可靠性。
4.典型场景:汽轮机中小叶片加工黑灯产线
痛点:汽轮机叶片加工目前仍多采用人工作业,效率和质量依赖操作者的经验与技术水平,存在人工成本高、误差大、效率低等问题,无法保证产品的合格率。
改造目标:建立针对汽轮机中小叶片自动化加工产线,实现24小时无人值守加工。
实现方式和需要条件:综合运用机内在线测量与自补偿、机内自动测刀、加工过程监控技术,代替人工测量补偿的过程,完成零件加工的自动化补偿。采用工业机器人和零点快换技术,并在产线内预设与自动导向车(agv)的接驳站,实现完全的自动化上下料和加工。以产线管控系统为核心,将制造执行系统(mes)、仓库控制系统(wcs)和智能agv贯通,实现多品种小批量汽轮机叶片的混线生产及无人值守加工。
5.典型场景:光伏组件数字化产线
痛点:传统光伏组件工厂大量依赖人工和经验,产品质量和生产过程一致性难以保证,而且数据共享难,协同效率低,影响生产能耗、产品质量和交付效率。
改造目标:通过产线数字化,实现资源管理、质量管理、生产管理等协同,提高制造效率。
实现方式和需要条件:在光伏组织制造车间,全面导入生产过程管理(mes)、仓储管理(wms)、设备管理(eam)、质量管理(qms)、数字化能源管理(ems)等软件,结合工业互联网、大数据、人工智能、数字孪生等新技术,开展产线物联网网络集成、设备和生产系统控制程序优化、ai技术与装备的有机融合,建立多系统集成的数字化产线,实现数据互联共享和协同制造。
6.典型场景:电力装备钢构部件柔性焊接
痛点:传统手工焊接焊缝质量不稳定,返工率高,焊缝成型外观差,而且焊接产生的强光和废气对人体伤害大,工作环境恶劣,影响焊接工人健康。
改造目标:打造基于数字化的焊接柔性线,以适应不同场景和空间,减少人工焊接量。
实现方式和需要条件:应用模块化和产线重构等技术,搭建柔性焊接产线。运用单悬臂焊接、双机器人悬臂焊接、小龙门焊接、大龙门焊接机器人,实现垂直焊和水平焊。根据焊缝大小和焊接材质不同,通过焊接机器人自动换枪,满足特殊位置、特殊材质焊接要求。
7.典型场景:高压开关关键零部件视觉对中装配
痛点:高压开关零部件存在尺寸偏差较大,目前多采用人工装配,可操作空间狭小、需多次人工调节,装配耗时耗力,同时易造成产品装配质量不一致问题。
改造目标:通过视觉引导装配技术实时调整位置进行自动装配。
实现方式和需要条件:通过搭建三工位壳体、动端装配的硬件平台及智能视觉引导装配系统测试平台,利用视觉引导技术实现三工位隔离开关壳体及动端的装配、硬件驱动控制、三维数据采集、引导数据计算、机械臂装配控制、数据镜像场景交互显示等功能,确保三工位隔离开关动端及接地端的三相对中,提高装配效率及装配质量。
三、质量管理
8.典型场景:汽轮机核心零部件质量管控
痛点:部分汽轮机生产过程的质量信息采用手工记录,执行效率低、信息记录不全,无法及时识别质量问题,质量追溯困难。
改造目标:实现质量全过程的精准追溯,提高质量管理效率,降低制造成本,提高产品质量。
实现方式和需要条件:针对汽轮机制造过程的质量检验,面向叶片、轮盘等核心产品,运用大数据、ai大模型等技术,搭建自动上下料、自动检测分析的一体化系统。构建数字化质量检验系统,实现检验计划、供应商监造、进货检验、制造质量管理、测量设备等平台化管控。将数字化质量检验系统与生产管控系统集成,打通质量数据链,构建质量管理统计分析、在线监控预警及质量协同改进的管控体系。
9.典型场景:变压器线圈视觉检测
痛点:变压器制造定制化程度较高,难以建立完善的视觉检测模型,目前视觉检测场景应用范围有限,识别精度低。
改造目标:通过新一代信息技术应用,实现关键生产环节自动检测,提升质量一致性。
实现方式和需要条件:以机器视觉技术为核心,通过光学、机械、电气、软件、算法的协调配合,开发高效、精确的线圈绕制综合在线检测装备,并通过结合ai机器视觉和3d扫描技术,实现线圈绕制的自动化检测和质量控制,提高产品质量、生产效率,降低成本。
四、产业链管理
10.典型场景:电力装备制造物料智能仓储物流
痛点:制造过程中的物料拣选和搬运流程过于繁琐,部分物料管理需要人工记录,速度慢、易出错。
改造目标:通过智能仓储物流系统,快速实现产品的出库,以及精准配送。
实现方式和需要条件:采用仓储管理系统(wms)系统,通过条码的应用,将物料从原料入库、上架、出库到成品出库进行全流程跟踪,精准监控物料的流转、半成品的转序以及成品的包装明细等信息。并将wms与agv通过接口进行对接,选择最优路线将物料自动配送到指定的工位,绑定搬运的物料信息与转序的单据,记录每道工序的产出以及接收情况,提升管理效率,提高物料送达速率和准确率。
11.典型场景:大型变压器制造资源协同
痛点:大型变压器制造周期长、零部件数量采购工作量大,难以进行批量化的生产组织,制约项目交付进度。
改造目标:通过协同制造,实现前端与营销、后端与供应商、订单与交付的打通,使产业链联动更加高效,优化资源配置。
实现方式和需要条件:建立物料、客户、供应商及其他基础数据统一资源管理平台,实现统一采购、统一生产、统一调配。整合分散的采购资源,提高供方合作质量,规范采购流程,优化采购成本,控制供应风险。实时监控采购绩效,全方位展示库存情况,有效控制库存水平、提高库存周转率,实现采购、库存与财务一体化。
五、运维服务
12.典型场景:风力发电场机组智能运维
痛点:传统的风电场巡检通常需要人工登塔,存在一定的安全风险,而且传统目视检查难以识别高段塔筒、风机叶片缺陷。
改造目标:通过新一代信息技术,实现塔筒、机组及叶片的远程监测和运维。
实现方式和需要条件:通过搭载摄像头和其他传感器的无人机,实时获取风电场的图像、温度、湿度等数据,实现对风机叶片、塔筒等部位的常规巡检,并配合风机自身状态数据ai信息对比,及时发现运行问题,运用爬塔小车和智能机器人,对风电装备进行远程检修,降低人工作业安全风险,确保风电场的正常运行。
13.典型场景:核电站仪控运行维护智能化平台
痛点:核电站各系统间接口复杂,没有统一的平台进行汇总和管理,不能直接展示问题原因、解决方法等,导致维护成本高、人力投入大等问题。
改造目标:建立核电领域专用的工业互联网平台,打破不同系统间的信息孤岛,对仪控系统全方位监视和统计分析,降低维护成本。
实现的方式和需要条件:通过解决核电厂海量实时数据处理、边缘数据采集、人工智能算法等技术,研究核电领域的工业互联网平台,采用“平台 app”架构,具备多源异构数据采集、海量数据处理、数据仓湖存储、智能算法、可视化展示等能力,提升核电厂系统的统一性,提高对系统运行、维护状态感知和决策能力。
14.典型场景:发电机组状态监测及智能预警诊断
痛点:当前大部分电厂数字化程度不高,底层基础设施仍采用传统信号处理方式,机组运行数据利用程度不高,机组运维数字化程度低,部分异常无法及时预警。
改造目标:实现发电机组在线状态监测及运行异常智能预警诊断。
实现方式和需要条件:运用大数据、人工智能、数字孪生等技术,开发汽轮机轴系故障、热力性能监测诊断、高温部件应力分析及寿命监测、回热系统预警诊断、润滑油系统预警诊断等系统,实现装备状态监测、能效分析、性能优化、故障预警、智能诊断功能,显著提升机组运行经济性、安全性、稳定性以及运维智能化水平。
15.典型场景:加工制造装备运行状态监控
痛点:部分企业对数控加工装备、焊接机器人、热处理炉等关键核心装备缺乏有效的监测手段,而且在装备故障发生后,缺少对故障分析、统计,无法复用故障处理经验。
改造目标:实现加工制造装备状态监测与控制,提高装备使用效能,保障制造过程安全可靠。
实现方式和需要条件:针对数控机床、机器人、焊机、热处理炉等关键核心装备,搭建车间物联网。开发统一的数据采集与监视控制系统(scada)系统,对装备运行时间以及生产过程中的状态参数、工艺参数、故障信息等进行实时采集。采集的各类型数据统一进入数据平台进行管理,实现与工艺要求的匹配性分析。建立装备关键参数等指标的监控策略,对装备故障、异常情况进行及时处理和调整。优化生产过程,提高装备使用效率,为车间排产及资源动态配置提供有力保障。
文章来源:中国电力设备网http://www.chinapower.com.cn/
最新案例
- 江苏南京开关厂110kvgis耐压试验圆满完成
- 10月23日,江苏南京开关厂成功完成了gis各项试验项目,gis作为电力系统中的重要设备,其性能和质量直接关系到电力系统的安全稳定运行。因此,对gis进行严格的试验和检测是确保其质量的关键环节。此次试验由木森运维专业团队在严格的安全措施和操作规程下进行,确保了试验的准确性和可靠性,据了解,南京开关厂股份有限公司,是专业从事变配电成套、元器件及智能化系统的研发、生产、安装、运维、销售服务。
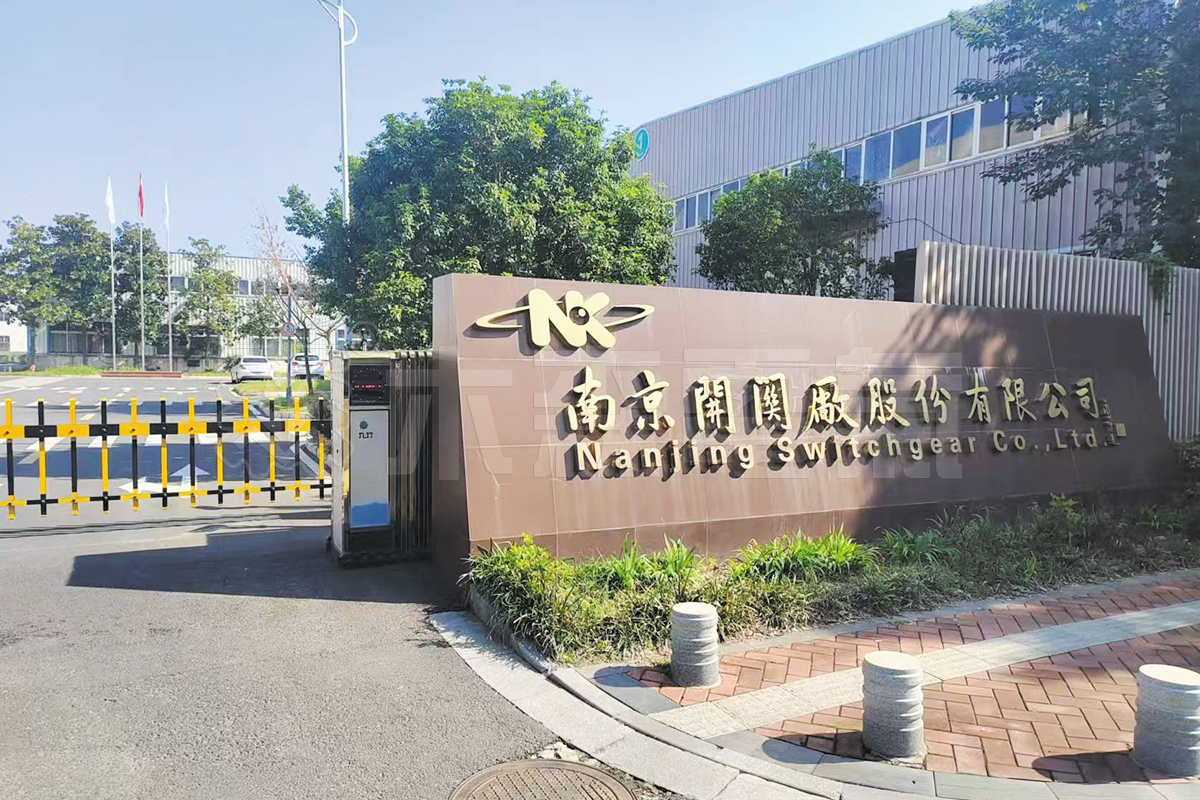
- 35kv祁家湾变电站断路器及电流互感器试验
- 35kv祁家湾变电站位于湖北省武汉市黄陂区祁家湾镇,祁家湾变电站主要负责将上级电网输送来的电能进行降压处理,然后输送到祁家湾镇及周边地区的用户端。项目名称为35kv祁家湾变电站更换一台断路器,1组电流互感器
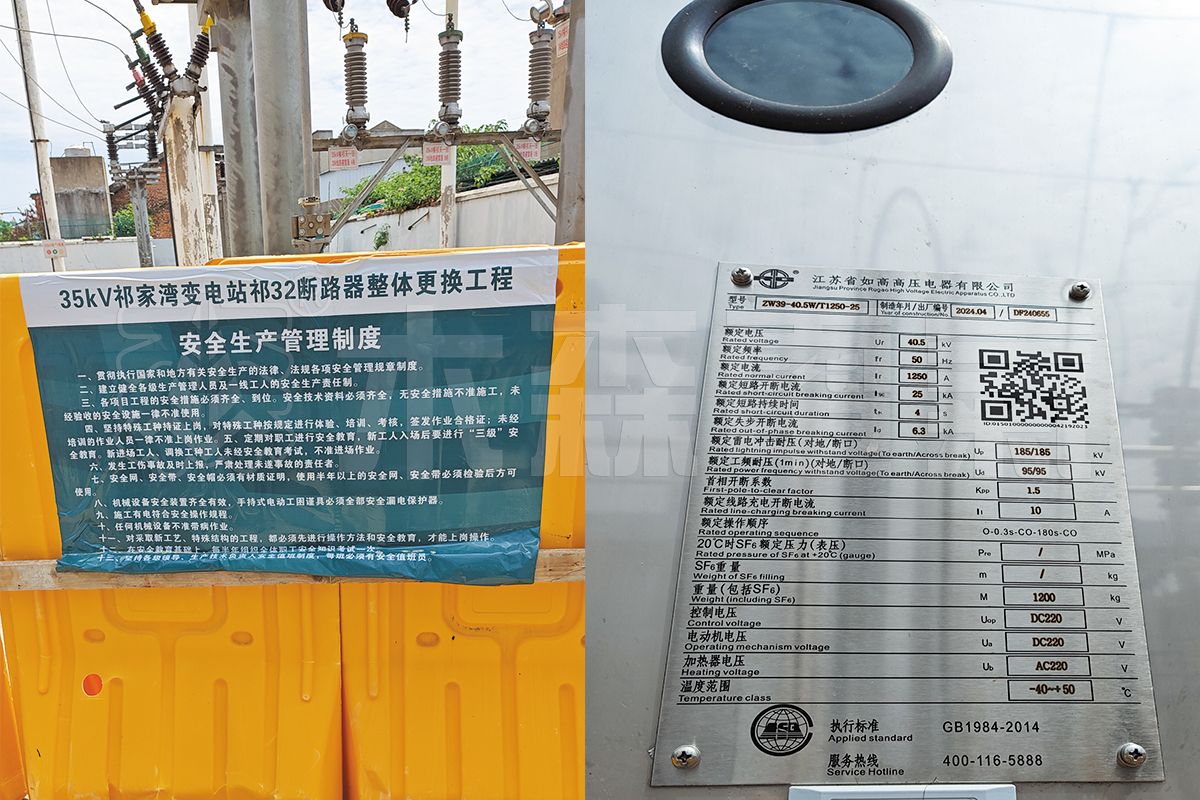
- 河南平煤神马东大化学有限公司变电站预防性试验顺利完成
- 河南平煤集团神马东大化学有限公司是一家以从事化学原料和化学制品制造业为主的企业,为应对即将到来的用电高峰,确保电力设施的稳定运行,该公司要求进行现场预防性试验。此次试验覆盖了该公司的关键电力设施,试验内容包括:110kv变压器2台、10kv及35kv柜18面、110kv间隔2个,旨在通过全面检查和测试,及时发现并处理潜在的安全隐患。2024年5月26日,我公司运维部分6名试验人员出发八朝古都河南开封,为河南平煤集团神马东大化学有限公司进行为期2天的2024年度变电站预防性试验。
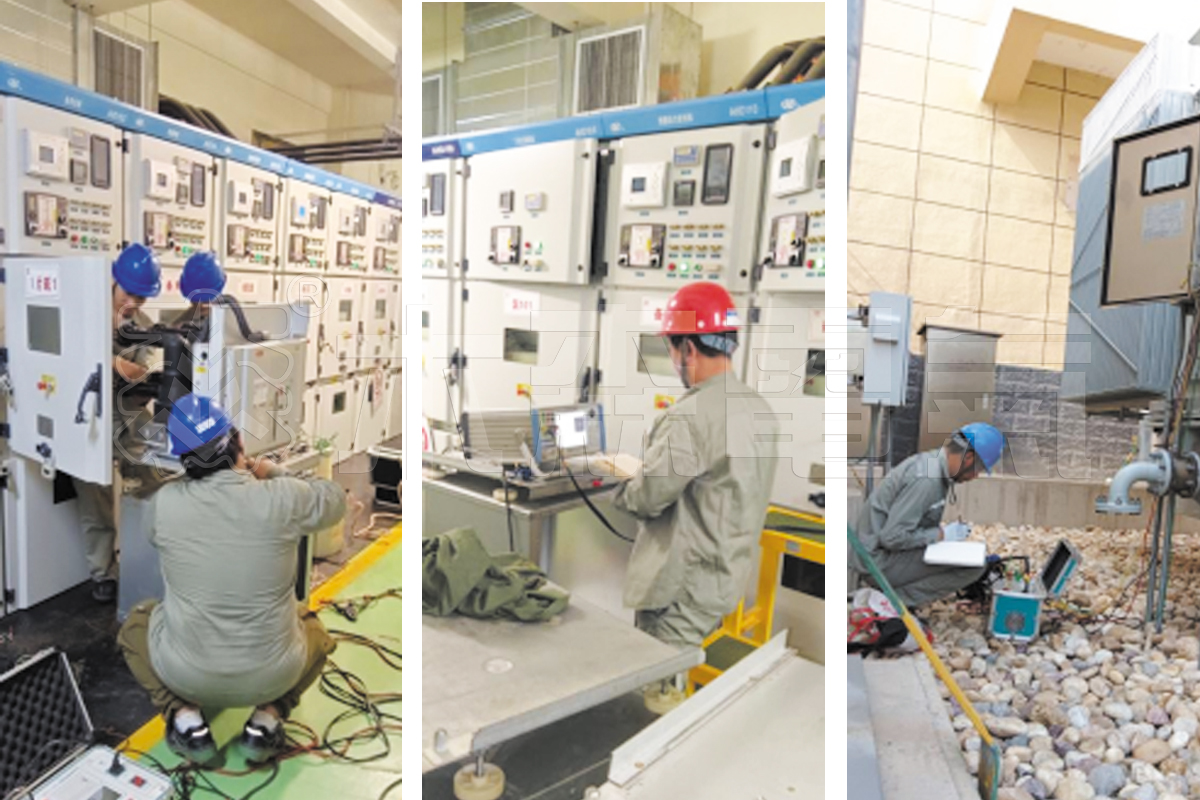